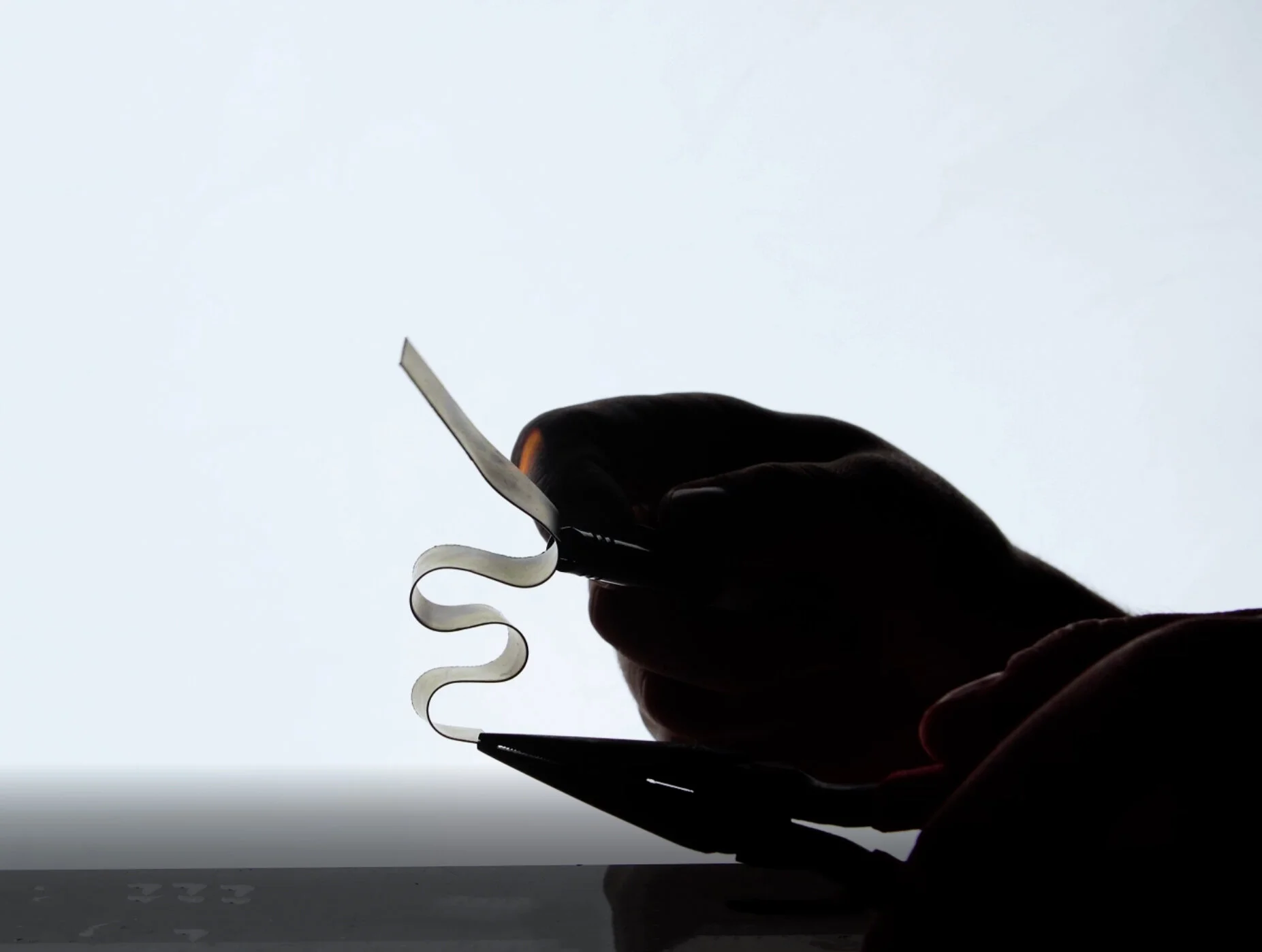
Shape Memory Alloy
Millipede
Shape memory alloys (SMA) are metal alloys with unique crystalline structures that allow them to be deformed at a low temperature and to return to their pre-deformed shape when heated. Typical SMAs are Nickel-Titanium, which is referred to as Nitinol. Below the transition temperature, SMAs are highly malleable - similar to solder wire in mechanical properties. Above the transition temperature, the crystalline structure of the alloy changes and the metal becomes stiff and springy, returning to its “memory state”.
The transition temperature is precisely set by the relative composition of the two metals. The memory state is considered a state of superelasticity, which means the metal can be deformed beyond its normal elastic range of motion and will still retain its pre-deformed shape. Take a slinky for example: a normal slinky is ruined when it gets stretched too far - the coils are no longer pitched against each other and the over-stretched area remains stretched. It has undergone plastic deformation, which occurs when a material is deformed beyond its elastic region. A superelastic slinky, in comparison, would return to its original shape even after it is deformed beyond its elastic range. In shape memory alloys, the cold state’s crystalline structure is referred to as martenisite while the memory state’s is referred to as austenite.
What is special about SMAs is that they can be “taught” a formal shape to return to in its memory state. Essentially, the SMA needs to “learn” its new orientation of atoms in the memory state. To do this, one must secure the SMA in its desired position and heat it uniformly to about 480°C. At first, the SMA will want to return to its previous memory position. After heating it for some time in a fixed, desired position, the atoms relax and rearrange to accommodate the new memory state. Once the SMA is heated in its new position to about 480°C and consequently quenched in cold water, it will once again become malleable and will only return to its new memory state once heated above its transition temperature.
It is important to note two considerations in this process. First, SMAs can cycle through transition states without fatigue. This means that SMA actuation mechanisms have a longer lifespan than most mechanical processes. Second, the transition occurs over the course of a temperature range. As the SMA approaches the transition temperature, the memory state is adopted slowly as all of the atoms in the alloy heat up. The transition is by no means instant. This latency is referred to as hysteresis. To reduce hysteresis, copper is added to the alloy mixture. To increase strength in its memory state, iron can be added to the alloy.
Roche Labs acquired samples of Nitinol in the form of springs, sheet metal, and wire of various gauges and transition temperatures from Kellogg’s Research Labs (an expert in SMA manufacturing). Using a heat gun to bring the Nitinol above its transition temperature, it became evident how metal thickness relates to the amount of heat needed to achieve transition. A small gauge spring will quickly return to its coiled state without much force, while a thicker spring may react more slowly, but with greater strength. Three transition temperatures were tested: 35°C (body temperature), 45°C, and 80°C. At room temperature (approximately 20°C), the lower temperature transition metals (35°C and 45°C) tended to be springier than the higher transition (80°C) samples. This is likely due to the hysteresis of transition metals, as the proximity to their transition temperature allowed some martensite to transition to austenite and begin to display superelastic behaviors.
Many SMA actuation mechanisms will incorporate a passive return mechanism to bring the system back to its initial “cold” state. Two-way shape memory is possible, but tends to be weaker and slower than typical one-way shape memory, so passive forces from springs or gravity are commonly used to return a system from its memory state to its initial state.
To conclude, shape memory alloys hold clear potential as actuation mechanisms in architecture. While it is difficult to achieve a tight transition at a specific temperature, the alloys can be actuated using electricity at a high power for a very short amount of time. In this case, the mechanism is still consuming low amounts of energy overall. We imagine these mechanisms could be implemented into louvered facades as a way to create adaptive facades that are passively temperature-responsive. Similarly, facades could be designed to adapt at highly specific temperatures using digital electronic control mechanisms that actuate the SMA. While the possibilities are seemingly endless, we are most excited about the possibility of maintaining thermal comfort of an interior without the need for energy-intensive mechanical systems. The autonomous mechanisms offer a sense of wonder and require one to reflect on environmental conditions in a way that is often overlooked in a fully climate controlled building. With this in mind, we see Nitinol not so much as a solution, but rather a critical component of a fully-designed system.
References
Kellogg, Joe. Nitinol in Plain Language. Kellogg’s Research Labs, April 2020.
Agrawal, Ashish and Dube, Ravindra Kumar. “Methods of fabricating Cu-Al-Ni shape memory alloys.” Journal of Alloys and Compounds, vol. 750, 2018, pp.235-247. DOI: 10.1016/j.jallcom.2018.03.390.
PI Sam Golini
Production William Kavanagh
Management and Media Gioia Connell